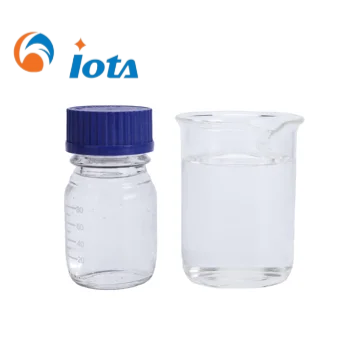
In modern industrial production and mechanical equipment operation, lubricating oil and grease play an indispensable role. They can reduce friction, reduce wear and extend the service life of equipment. Dimethyl silicone oil, as a synthetic lubricant with excellent performance, has been widely used in the field of lubricating oil and grease due to its unique chemical structure and physical properties. However, choosing dimethyl silicone oil with appropriate viscosity is crucial to achieve the best lubrication effect.
For lubricating oil, the choice of its viscosity mainly depends on the working conditions of the equipment, such as temperature, speed and load. In low temperature environment, low viscosity dimethyl silicone oil is required. Low viscosity dimethyl silicone oil (generally refers to 5-50cst) has excellent low temperature fluidity and can quickly reach various lubrication parts in cold environment to ensure smooth start-up of equipment. For example, in some precision instruments and meters, due to the extremely high precision requirements of its components and the possibility of working in low temperature environment, low viscosity dimethyl silicone oil can ensure the normal operation of the instrument and reduce the wear caused by starting difficulties. At the same time, low viscosity dimethyl silicone oil can also reduce fluid resistance, reduce energy loss and improve the operation efficiency of equipment.
Under high temperature and high load working conditions, high viscosity dimethyl silicone oil is more suitable. High viscosity dimethyl silicone oil (500cst and above) can form a thicker lubricating film on the metal surface, provide stronger load-bearing capacity, effectively resist the damage of high temperature and high load to the lubricating film, prevent direct contact between metals, and thus reduce wear. For example, in the gearbox of large industrial machinery, since the gears are under great pressure and friction when running at high speed, and a lot of heat is generated, high viscosity dimethyl silicone oil can maintain good lubrication performance under such harsh working conditions and ensure the stable operation of the equipment.
Grease is composed of base oil, thickener and additives. When dimethyl silicone oil is used as base oil, its viscosity selection is also closely related to the use scenario of the equipment. In some occasions where long-term lubrication is required and it is not easy to replenish lubricants, such as automobile wheel hub bearings, medium and high viscosity dimethyl silicone oil (50 - 500cst and above) is more suitable. Medium and high viscosity dimethyl silicone oil can be better combined with thickeners to form a stable structure, so that the grease has good adhesion and anti-loss properties, can adhere to the lubrication parts for a long time, and continue to play a lubricating role.
In addition, for some applications that have high requirements for the low-temperature performance of grease, such as some equipment in the aerospace field, low-viscosity dimethyl silicone oil can be used in combination with a suitable thickener to prepare a grease that still has good fluidity and pumpability at low temperatures, meeting the lubrication needs of equipment in extreme environments.
In summary, when selecting the viscosity of dimethyl silicone oil in lubricating oils and greases, it is necessary to comprehensively consider multiple factors such as the operating temperature, speed, load, and use environment of the equipment. Only by selecting dimethyl silicone oil with a suitable viscosity can its excellent lubrication performance be fully utilized, providing reliable protection for equipment, improving the operating efficiency and service life of equipment, reducing maintenance costs, and helping the efficient development of various industries. In the future, with the continuous advancement of materials science and lubrication technology, the application of dimethyl silicone oil in the field of lubricating oils and greases will continue to expand and optimize, providing better solutions for equipment lubrication under more complex working conditions.