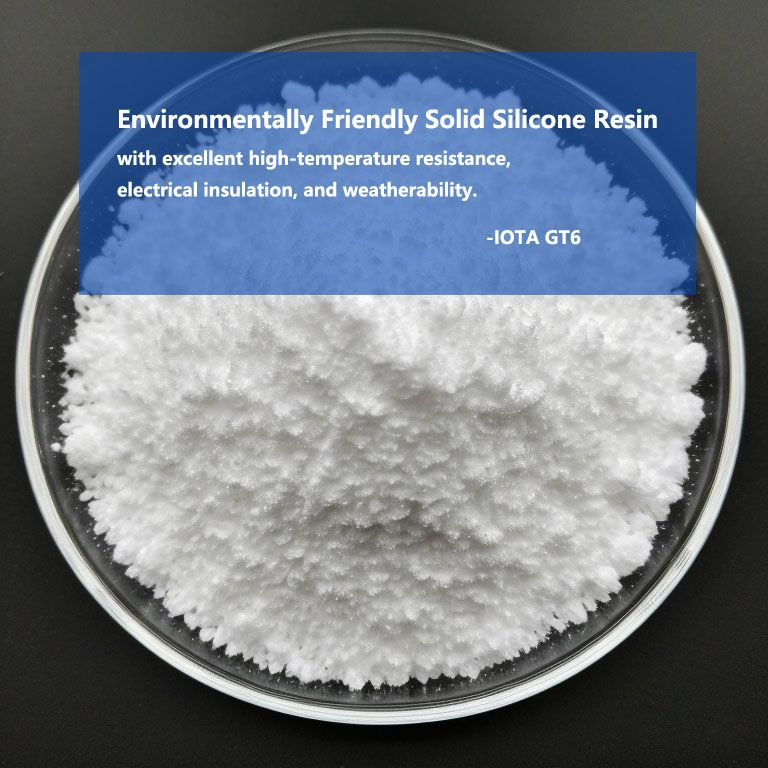
1. Introduction
Resins play a pivotal role across diverse industries, serving as essential components in coatings, adhesives, and composites. Among the vast array of resins, organic silicone resins possess unique characteristics that set them apart from general resins. These differences are deeply rooted in their chemical structures, which in turn give rise to distinct property profiles and application domains.
2. Chemical Structure
2.1 Organic Silicone Resins
The backbone of organic silicone resins is characterized by silicon - oxygen (Si - O) bonds. Silicon, a semi - metal, forms robust covalent bonds with oxygen. Attached to the silicon atoms are various organic groups, such as methyl (CH₃), ethyl (C₂H₅), phenyl (C₆H₅), or vinyl (CH₂=CH -). For instance, in polydimethylsiloxane (PDMS), a prevalent silicone polymer, methyl groups are linked to the silicon atoms within the Si - O backbone. This amalgamation of inorganic Si - O chains and organic side - groups results in a hybrid structure. The Si - O bond, with a bond energy of approximately 452 kJ/mol, contributes significantly to the resin's stability.
2.2 General Resins
General resins, including epoxy, polyester, and acrylic resins, typically feature a carbon - based backbone. Epoxy resins, for example, are centered around epoxide groups, which are carbon - containing functional groups. The carbon - carbon and carbon - oxygen bonds in these resins exhibit different bond energies compared to the Si - O bonds in silicone resins. In acrylic resins, the backbone is formed through the polymerization of acrylic monomers, which predominantly consist of carbon - carbon double - bond - containing molecules. This carbon - based structure often leads to varying reactivity patterns and physical properties.
3. Thermal Properties
3.1 Organic Silicone Resins
Organic silicone resins are celebrated for their exceptional thermal stability. Thanks to the strong Si - O bonds, they can endure elevated temperatures without substantial degradation. Many silicone resins can maintain their mechanical and chemical integrity at temperatures ranging from 200 - 300°C continuously. Some specialized silicone formulations can even withstand temperatures as high as 500°C or more in specific applications. This makes them ideal for high - temperature environments, such as in aerospace engine components, where materials must resist extreme heat.
3.2 General Resins
Conversely, most general resins have relatively lower thermal stability. Epoxy resins, for example, usually start to degrade at temperatures around 150 - 200°C, depending on the formulation. Polyester resins also have limited heat resistance, and prolonged exposure to high temperatures can cause them to soften, lose mechanical strength, and even decompose. Acrylic resins, although suitable for a variety of applications, are not well - adapted to high - temperature environments and may experience yellowing, embrittlement, or loss of adhesion at relatively lower temperatures compared to silicone resins.
4. Hydrophobicity
4.1 Organic Silicone Resins
The presence of non - polar organic side - groups, particularly methyl groups in many silicone resins, renders them highly hydrophobic. This hydrophobic nature confers excellent water - repellent properties. When applied as coatings, silicone resins can prevent water absorption, safeguarding substrates from moisture - related damage, such as corrosion, mold growth, and the degradation of organic materials. For example, silicone - based waterproofing coatings on buildings can effectively repel water, keeping the interior dry.
4.2 General Resins
General resins vary in their hydrophobicity. Epoxy resins, when appropriately formulated, can possess some water resistance, but they do not match the hydrophobicity of silicone resins. Polyester resins are often more hydrophilic than silicone resins, making them susceptible to water absorption, especially in humid environments. This can lead to issues such as swelling, reduced mechanical strength, and the growth of mold or mildew on the surface of objects coated with polyester - based materials. Acrylic resins also exhibit different degrees of water resistance, but they generally do not reach the high - level hydrophobicity of silicone resins.
5. Chemical Resistance
5.1 Organic Silicone Resins
Silicone resins demonstrate good chemical resistance against a broad spectrum of chemicals. The Si - O backbone is relatively stable and resistant to attack from acids, bases, and many organic solvents. However, the degree of chemical resistance can be tailored by modifying the organic side - groups. For example, resins with fluorinated organic side - groups exhibit enhanced resistance to aggressive chemicals, making them suitable for use in chemical processing plants.
5.2 General Resins
General resins have diverse chemical resistance profiles. Epoxy resins are known for their good resistance to many chemicals, but they may be sensitive to strong alkalis. Polyester resins can be degraded by some acids and alkalis, and their resistance to organic solvents can also be limited. Acrylic resins, while resistant to many common substances, may not be as chemically resistant as silicone resins in highly corrosive environments.
6. Surface Tension and Adhesion
6.1 Organic Silicone Resins
Organic silicone resins have a low surface tension, enabling them to spread easily over surfaces. This property is advantageous in coating applications as it facilitates the formation of smooth and uniform films. However, their low surface tension can sometimes pose challenges in achieving strong adhesion to certain substrates. Special surface treatments or the addition of adhesion - promoting agents are often necessary to enhance the adhesion of silicone resins.
6.2 General Resins
General resins typically have higher surface tensions compared to silicone resins. Epoxy resins, for instance, can have excellent adhesion properties to a variety of substrates due to their ability to form chemical bonds with the surface. Polyester and acrylic resins also generally exhibit better inherent adhesion to many materials without the need for extensive surface modification in most cases.
7. Application - Field Comparison
7.1 Organic Silicone Resins
-
Aerospace and High - Temperature Industrial Applications: Due to their high thermal stability, silicone resins are extensively used in aerospace components like engine parts, exhaust systems, and high - temperature seals. In the industrial sector, they are applied in furnaces, ovens, and high - temperature pipelines. Their ability to maintain performance under extreme heat ensures the safety and efficiency of these systems.
-
Waterproofing and Moisture - Sensitive Applications: The high hydrophobicity of silicone resins makes them ideal for waterproofing applications. They are used in roofing materials, waterproof coatings for buildings, and protective coatings for electrical components in humid environments. Their water - repellent properties prevent moisture - induced damage, extending the lifespan of the protected materials.
-
Medical and Food - Contact Applications: Silicone resins' biocompatibility, chemical stability, and low toxicity make them suitable for medical devices such as catheters, breast implants, and food - contact surfaces. They can withstand sterilization processes and maintain their integrity in contact with biological fluids or food products.
7.2 General Resins
-
Construction and Adhesive Applications: Epoxy resins are widely used in construction for flooring, coatings, and adhesives. Their good adhesion, chemical resistance, and mechanical strength make them suitable for bonding various materials, such as concrete, metal, and wood. In the adhesive industry, epoxy - based adhesives are popular for their high - strength bonding capabilities.
-
Automotive and General - Purpose Coatings: Acrylic resins are commonly used in automotive coatings, providing a durable, glossy finish. They are also used in a wide range of general - purpose coatings for furniture, appliances, and consumer products. Their relatively low cost, good color retention, and ease of application make them a preferred choice for these applications.
-
Composite Manufacturing: Polyester resins are extensively used in composite manufacturing, especially in the production of fiberglass - reinforced composites. They are used in boat hulls, automotive body parts, and building panels due to their relatively low cost, good mechanical properties, and ease of processing.
8. Conclusion
In summary, organic silicone resins and general resins exhibit significant differences in their chemical structures, thermal properties, hydrophobicity, chemical resistance, surface tension, and adhesion. These differences translate into distinct application areas. Organic silicone resins excel in high - temperature, water - repellent, and biocompatible applications, while general resins, with their diverse property profiles, are well - suited for a wide range of construction, automotive, and composite - manufacturing applications. Understanding these distinctions is crucial for industries to select the most appropriate resin for their specific requirements, ensuring optimal performance and cost - effectiveness.